Our custom-built Multifoil Machine is one of the single greatest investments we’ve ever made into our business. Which is a good thing, given that we spent HALF A MILLION POUNDS on designing, developing, and building the beauty, all told.
We’ve shown you the incredible results of that investment before, and we’ll no-doubt show them to you again. However, today we wanted to do something a little different. Instead of talking about our fantastic multifoil machine, we’d like to tell you all about the process of designing, developing, and ultimately building this massive project.
But to do that properly, we needed some professional insight into what goes into an undertaking like this, which is exactly why we sat down for an interview with Ian Haigh, managing director of Engenios Mechanica; the very team that built our new machine for us.
Who Are Ian Haigh and Engenios Mechanica?
When we decided that we wanted to begin work on our custom-made multifoil machine, we knew that we were going to need expert support — the vast majority of which came from Ian Haigh and Engenios Mechanica. But let’s hear from Ian about what they do…
“We build bespoke manufacturing equipment and automated production lines for pretty much anything you could put inside a factory really.”
And Ian is exactly the man to be managing director for a business like this, considering all of his experience in the industry…
“I’ve been in mechanical engineering my entire career. I’ve been involved with machine building at all levels, from the very bottom to the very top, including implementing it and improving it, developing it, making it work, buying it, and actually building it.”
And it’s clear to see how all of that experience and expertise is an ideal fit for Engenios Mechanica which, as Ian explains, has a particular focus on creating bespoke solutions to help automate and optimise vital elements of production processes.
“As a company, we like to take processes that need automating, design and build a machine specifically for that job, and then develop it to get the optimum throughput from that machine.”
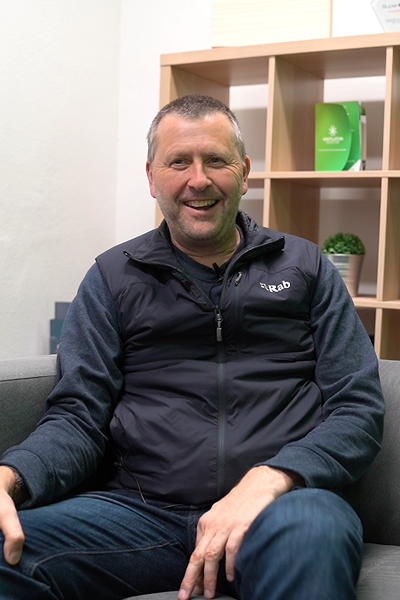
Understanding all of that, it’s pretty clear to see why Engenios Mechanica was nothing less than a perfect fit for our goal of developing and building a custom-made machine to help us revolutionise our local production facilities; which is why you might be interested to hear that, just over 2 years ago, Ian and his team at Engenios Mechanica weren’t who we first reached out to when we decided to create our £500K Multifoil Machine.
How It Started…
In fact, we were working with a company called Control Freaks, who specialise in (no big surprise here) control systems, which are essentially a collection of controls built into machines like this to allow “human-machine interface” as Ian puts it. But why weren’t we working with Ian’s team?
Well, the answer is pretty simple. We had never worked with Engenios Mechanica before, so we simply weren’t aware of how well suited they were to the work we needed to do. Control Freaks of course, were perfectly suited for an incredibly important element of the project, and so we contacted them first.
That does, however, leave one question unanswered: How did we begin working with Ian and Engenios Mechanica? Well, we found that Ian explained the whole process quite well during our interview…
“We were initially brought in through a control system company called Control Freaks, who were contacted by SuperFOIL to look at this job. But they specialise in control systems and they really needed someone to do the mechanical design and take on the whole project and run it as a project. We’ve worked quite closely with Control Freaks in the past, so they asked us to get involved.”
It’s as simple as that. Control Freaks had worked with Ian’s team in the past and knew that they were the perfect fit for our project, and so they put us in touch with one another. Engenios Mechanica ran the project and worked closely alongside Control Freaks who put “the brains of the machine together” and gave it “the instructions for what to do in certain circumstances” as Ian explained.
And this was absolutely one of the first and best lessons to learn from this project: the most reliable professionals are the ones who’s reputations and professional relationships speak for themselves.
We knew we could rely on Engenios Mechanica before we ever met them, because of the trust and respect that they had cultivated through their work alongside Control Freaks; and those are the sorts of qualifications that you can really trust.
Ian’s Insights into the Design Process
“Nearly two years,” that was Ian’s response when we asked him how long his team had spent on the design process for our custom-built production machine. He goes on to clarify that…
“Of course, that wasn’t continuous. There were patches at the start of the project when it would have been continuous. But, because of the iterative process of trying things, and then going back to the drawing board, and doing some redesign — the design doesn’t really stop until you get a finished machine“
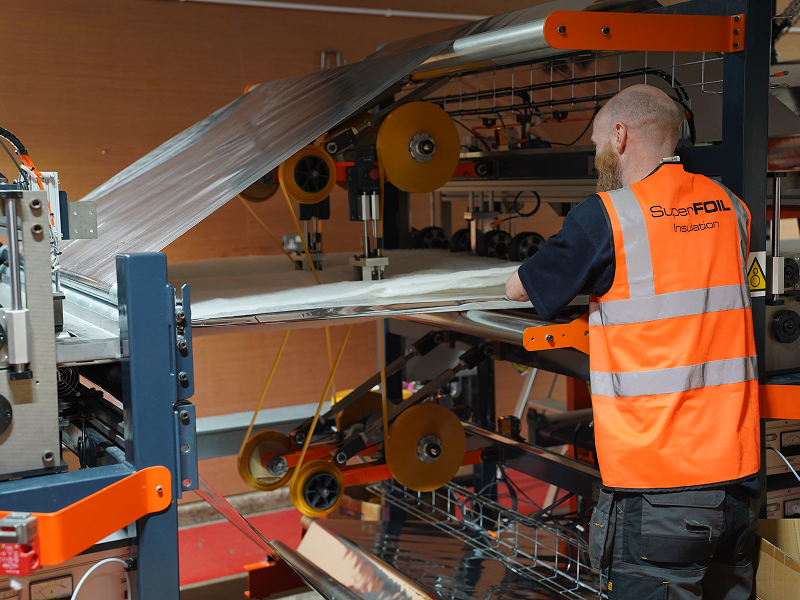
This “iterative process” of design is really fundamental to the creation of a custom-built, top of the line machine; and that was exactly what we were after. Of course, there are ways to streamline this process and ensure that things are done as efficiently as possible.
For example, Ian took the time to explain the importance of developing a “full concept” before diving too deeply into your design process.
“That’s really hard to do if you do things bit by bit by bit. What you tend to find is you build one module, then you build the next one and attach it […] and think,
‘Ah, yeah. There’s a better way of doing that first module.’
And you end up going back and back around this loop. And if you do it that way, it takes a really, really long time.”
And these kinds of issues are exactly where you can end up losing a lot of time when designing bespoke machinery meant to cover quite a few functions for your production line. Fortunately, Ian has a better way:
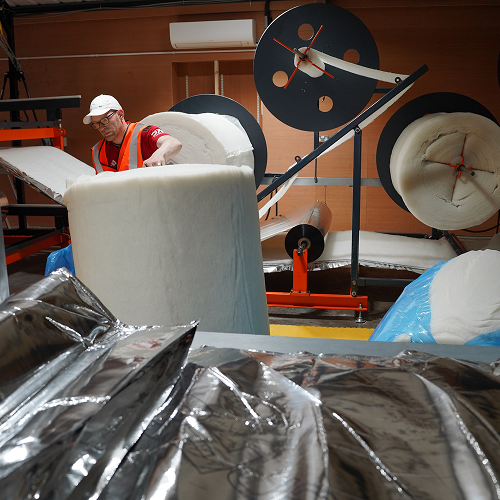
“Getting a full concept from the start, and working out how the whole thing is going to link together and flow together, […] you know that that’s going to work and you can make small changes to each thing along the way individually that doesn’t have a knock-on effect on the next thing further down the line.”
Just one simple adjustment in mindset, and you can save yourself a lot of time and trouble during your design and development process. However, even with the best techniques in the business, the reality is this:
If you want to get the very best result, then you absolutely must be prepared to spend as much time as necessary to get that result.
Innovation and improvement are fundamental elements of the design process, as is testing and iteration, and they All. Take. Time.
Regardless of if you make the same decision we did and decide to let the process take as much time as necessary, before too long you’re going to begin incorporating more than just design into the development of your new equipment.
So let’s take a look at what Ian had to say about the next part of the process…
Breaking Down the Building Process
As incredibly important as an effective design is to the development of custom-equipment like this, at the end of the day a design is just a set of instructions on how to create something, which means it’s only useful for one thing.
Building.
And when you’re working to develop bespoke equipment for your business, you’re always going to start with building prototypes.
Fortunately, Ian had plenty of insights to share about the process of prototyping and building our custom multifoil machine, and pretty much any kind of equipment you could think of. So let’s hear what he had to say on the topic…
“What we would normally do is we would start off by identifying all the individual operations in the process. Putting those together into a sequence and into a sort of basic concept of a machine. And then what we would do for each one of those operations, if you like, such as the welding, that would be an operation in its own right.“
“We would come up with a conceptual method for each of those. Try it and test it first to make sure that it worked. And then we would design a module for each of those things. Build the whole thing, but build into it enough flexibility to change things along the way. And then test it and test the thing (the multifoil machine) as a whole.”
By taking this approach, you gain a lot of individual control over each process that the machine is responsible for, and ensure that they are all optimised carefully. Plus, at the same time you can work a lot of flexibility into your design and building process, the importance of which we’ll discuss in detail soon.
Suffice it to say, however, that the combination of granular control AND flexibility is a huge benefit to getting exactly what you want out of the machine, and Engenios Mechanica‘s ability to incorporate both with skill was a testament to how much they really brought to this project. Of course, no benefit ever comes completely free from drawbacks, which is why Ian went on to explain that…
“With that kind of approach there’s always going to be […] after the machine is actually built and runnning, quite a lot of tweaking, changing things, development, watching what happens and trying to ensure that the quality of the product doesn’t fall down at any point”
That being said, we believe that innovation and improvement isn’t something you should ever stop doing within your business; which meant that this tradeoff felt like a small price to pay for so much benefit.
So, now that you know how we approached both the building and design processes for this project, it’s time we dive into one of the most interesting elements… how we brought the two together!
Bringing It All Together & How Building Defines Design
The relationship between building and design custom equipment like this is utterly fascinating. As we’ve already mentioned, the design process for this project took years, and this drills down to the heart of why.
You see, when you’re building something from scratch, something “that’s not been done before” as Ian puts it, there is inherently going to be a lot to learn.
- What is the best way to approach a problem?
- How can you most effectively incorporate something new?
- What is the impact of making a tweak here or a change there?
For many of these questions, the only way to really find an answer was to make an educated guess, build a prototype, and find out if you were right.
But, obviously, it didn’t make sense to build a brand new prototype for every single question we ran into, which introduced a fascinating balance to the equation: how can we learn as much as possible from each and every prototype? It’s incredibly hard to strike that balance properly.
Fortunately, Ian and his team have a brilliant design philosophy that helps to address this issue and kept the development of the machine moving forward, even as we were navigating new ground with every step we took.
And the truly fascinating thing, was that the first thing to do was actually to stop and see what we could learn from technology that already existed…
“Look at what technology was already out there and see if there’s anything we could take from that. And then the next step is to look at processes that are similar, probably not the same product or even the same material, but have similar demands and see what can be taken from that.”
After all, there is no sense in re-inventing the wheel when there could very well be plenty of inspiration to be found by considering technology that already exists. And in doing so, you actually massively reduce the number of guesses and assumptions you have to make, because you’re relying on concepts and equipment that already exists, even if you’re planning to apply it differently.
“And there’s things you can learn from other projects that we’ve done in the past. For example, in the past, we’ve worked a lot on wire handling equipment and equipment for manufacturing springs, that sort of thing. And there’s quite a lot of crossover really between that and handling foil.”
“We’ll gather ideas from there, evaluate them, and eventually we sort of hone it down to one likely candidate and do some testing.”
By relying on innovative applications of existing technology, and the concepts that underpin the machinery in other fields, you can reduce a lot of the guesswork that goes into developing custom-built equipment like this.
However, you won’t always be able to rely on tech that already exists. So, what does Ian’s team do when they need to work on genuinely new ground, developing bespoke processes from the ground up? Well, he explained their philosophy around that too…
“If you’re designing a new process from scratch, it’s quite important to give yourself that kind of flexibility. Otherwise, you end up going down dead end avenues where you get to a point where there’s absolutely nothing you can do. And the only thing you can do is to go back to the drawing board completely, start again and build an entirely new module.”
“But obviously doing that costs an awful lot of additional money and takes a lot of extra time. So it’s a non-starter. So you have to really give yourself, build yourself something that’s easy to change and adapt.”
As Ian explained, flexibility is the secret to succeeding in this kind of innovation. Flexibility in where you find your inspiration, but also in how you are developing your machine. There is no substitute for the ability to adapt to changing circumstances, especially when it comes to blending the idealism of your design with the reality of prototyping and building an actual product.
And we should know, after all, we went through this entire process as we developed our state of the art multifoil machine, spending half a million pounds and making more improvements and innovations than we can count.
So before we round things off with a quick list of our biggest takeaways, why don’t we hear from Ian about how he felt about finally delivering our finished multifoil machine, £500,000 and almost 2 years after we first started the process…
How It’s Going…
“Transporting it all here was quite nervous. Obviously, we brought all the parts up on a lorry, but just getting it here and not damaging it in transit was a big worry for me.”
“And sort of getting it into the factory and installed without breaking anything or causing any problems was a worry. So once we’d done that and we got it installed, yeah, that was a big relief and felt like a big step had been achieved.”
“That really was a big milestone in the project for us […] it seemed like a long time, and it must have seemed a long time to you guys as well before you were going to get it. So actually delivering it and installing it felt like a real success.”
“And that did work quite well, actually. There was a lot of effort went into it, but it’s nice to see, you know, something that’s such a challenge actually come to fruition and work.”
You can actually see the moment that all of our efforts came to “fruition” for yourself too, since we’ve put together a video on our YouTube channel to take you through the whole process, which you can watch right here:
Of course, installing the machine was far from the end of our journey to improve our local production capabilities. After all, as Ian says…
“There’s always things that need to be developed and changed, particularly with something that’s as brand new as this is.”
Which is why we’re still working with Ian and Engenios Mechanica to continue improving this fantastic machine, even to this day…
Our Key Takeaways
So, now that we’ve taken you through the whole process, and gotten some incredible insights from the mind of the man that made SuperFOIL’s incredible multifoil machine a reality, we thought it’d be best to end off with a few of our key takeaways from this process.
After all, Ian made a great point when he spoke about learning from previous experiences, so why not take this opportunity to learn from ours, and find out what we found most important about this process; both from our conversation with Ian and from having gone through the process ourselves!
1. Build a “Full Concept” Plan
Ian touched on how much of an impact this can have during our interview and we have to say, we agree completely. After all, a “full concept” mindset is downright essential to the success of any large project like this, particularly if you’re going to spend multiple years working toward a single goal.
You see, it’s all too easy to fall into the trap of working on one thing at a time, dealing with problems as and when they occur, and adopting an entirely reactive approach to a project like this.
However, as Ian points out, this requires you to spend far, far more time on your project. Instead, if you can outline everything you hope to achieve right away — giving yourself the “full concept” from the start — then you can approach every task with the knowledge of how it is all supposed to come together at the end.
This approach allows you to plan for the future, and massively reduces the time AND work required to reach a final, cohesive conclusion to your project. Even better, it often results in systems that are inherently more synergistic, because they are designed to work together, not forced to.
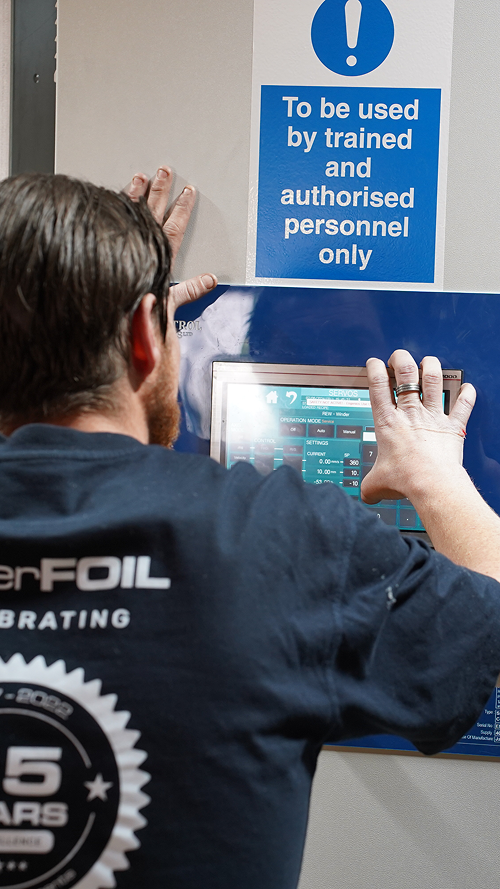
2. Keep Things Flexible
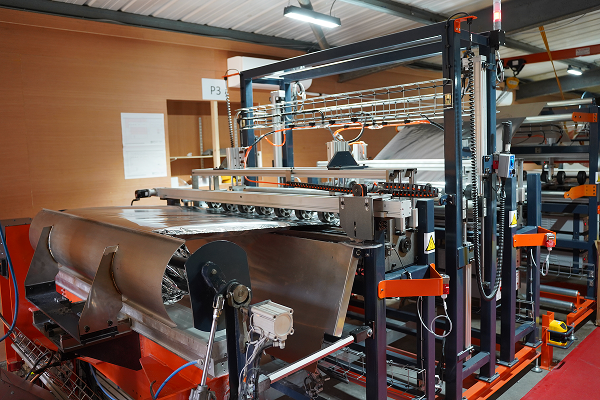
We’ve mentioned this idea already, but it really does bear repeating: flexibility is the key to effective innovation and the development of anything new.
After all, the ability to adapt to and incorporate new information and ideas into your design is essential — and the flexibility to consider different ways to achieve the same goal are all foundational to developing something that can be considered truly innovative.
As Ian warns, a lack of flexibility in your design process can lead you down “dead end avenues where you get to a point where there’s absolutely nothing you can do” and that’s one of the worst possible results when designing and developing something like this can be such a costly investment.
So remember, flexibility — both in your design and your thought process — is key!
3. Expect Trials and Errors
We haven’t really been shy about the fact that the process of developing this new machine was a long and expensive one. It was, of course, well worth the investment — but that doesn’t mean that it was easy to wait through the years of design, development, prototyping and COST.
So, if you do decide to engage with a similar project yourself, try to keep in mind that trials and errors are part of the package with this kind of project. And if you can hold out long enough to benefit from making mistakes and trying out new ideas, you will always have a better product by the end of it.
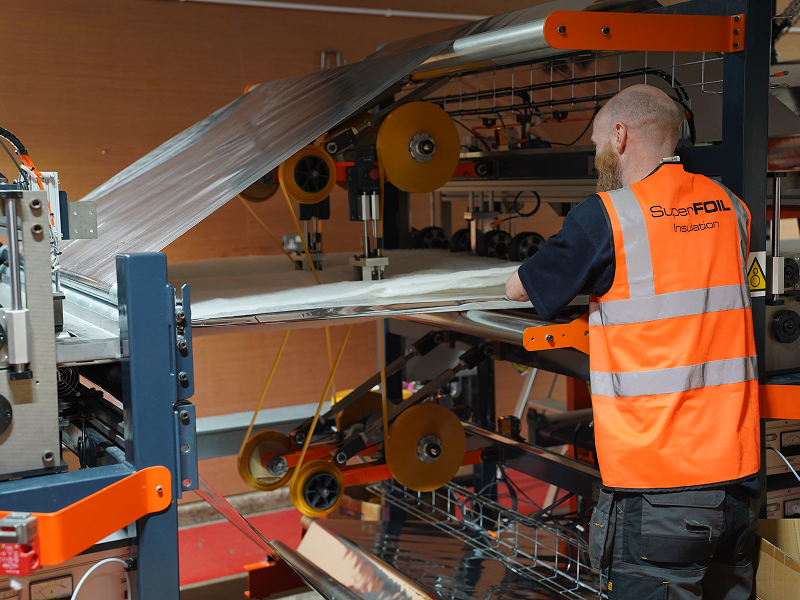
It’s a tricky balance to strike, of course, but worth the effort to get it right!
And, finally, the absolute most important point if you want to find success when developing your own purpose-built machinery for your production process…
4. Work With An Expert!
We would never have been able to achieve half the things we did on this project without the incredible knowledge, support, and capabilities of both Ian Haigh’s Engenios Mechanica and the amazing experts at Control Freaks too!
Ian made it clear that he and his team worked hard to integrate the wealth of knowledge that Will Bown, our CEO, brought to the table:
“He was involved right from the start and gave us guidance on the current process. And came up with various ideas and concepts, which were all sort of put into the pot. And between us, we sort of came up with a front runner in each case and went with that. And that’s how we like to work.”
After all, as Ian says we “know (our) product better than anybody else does”, but there really is no substitute for the skills and knowledge that come from a lifetime of experience with engineering, which is why Ian and his team at Engenios Mechanica were essential in taking this project from an ambitious dream to an achievement that we can truly pride ourselves on.

So, if you’re considering developing your own purpose-built machinery and you only take one piece of advice away from this post, make it this one: work with an expert!
Want to See More Like This?
If you’ve enjoyed this post and you’d like to see more like it, then filling out the form below is the best way to make sure that you’re the first to hear when we publish new blog posts like these.
But you don’t have to wait around for our next post either, we’ve published plenty of content over the years, and it’s all available to read on our website.
So, if you’d like to find out more about multifoil, the insulation industry, and the many real world examples of SuperFOIL products making a difference, then our News page is the perfect place to start!